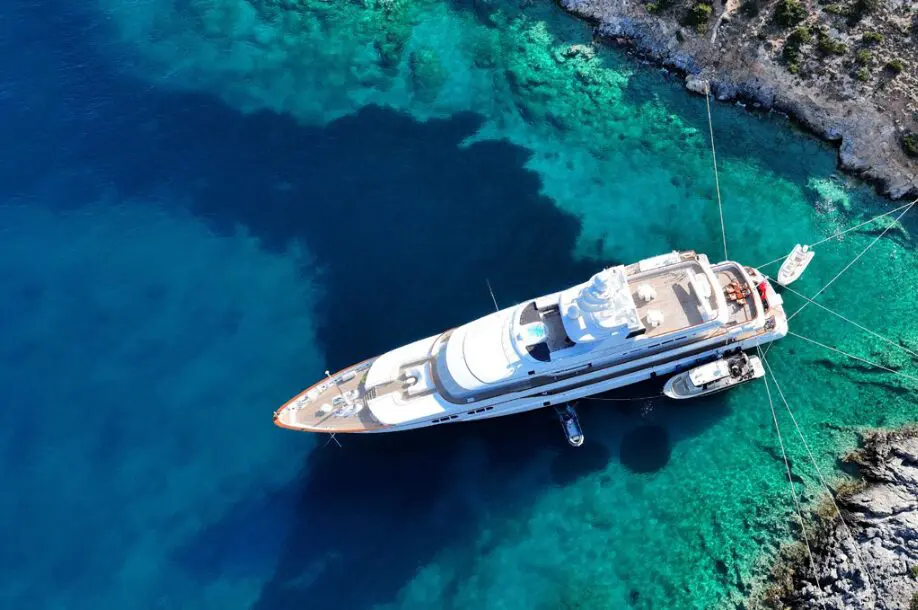
Marine composite materials have revolutionised the way boats and yachts are built and maintained. The principle behind their development stems from the age-old idea that “necessity is the mother of innovation.” Over the last century, marine composites have been developed both by design and chance, offering engineers and designers materials that improve performance, longevity, and aesthetics. Let’s look at the qualities that make these materials ideal for marine use and explore some of today’s most widely used composites.
Seven Essential Qualities of Marine Composites
Marine environments demand a lot from any material used in boat building or repairs. To meet these demands, composite materials used in marine applications must possess a combination of the following qualities:

Corrosion Resistance: Marine composites are resistant to rust and corrosion, ensuring longevity in harsh saltwater environments.
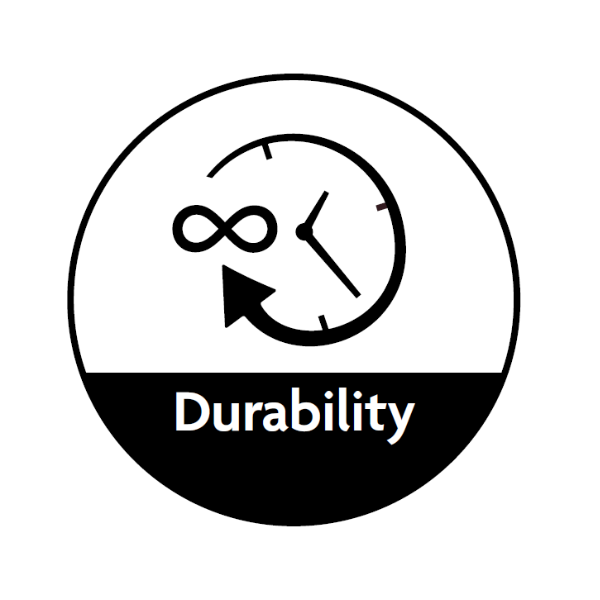
Durability: With the ability to withstand wear and tear over long periods, marine composites offer extended service life.
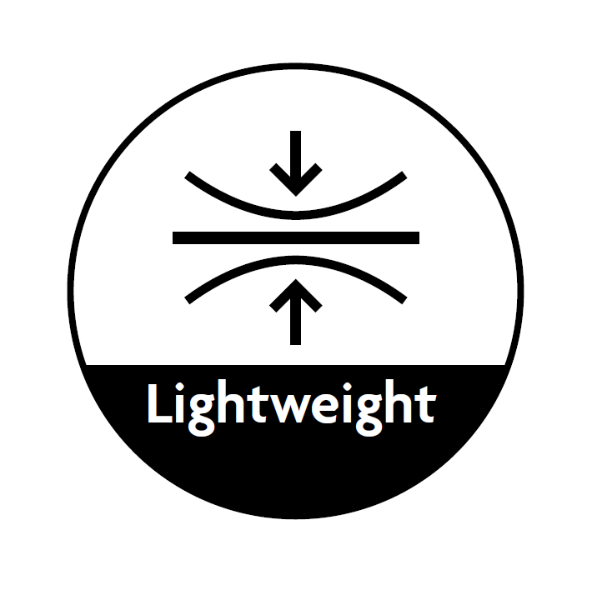
Lightweight: These materials are significantly lighter than traditional metals, which improves fuel efficiency and enhances boat performance.
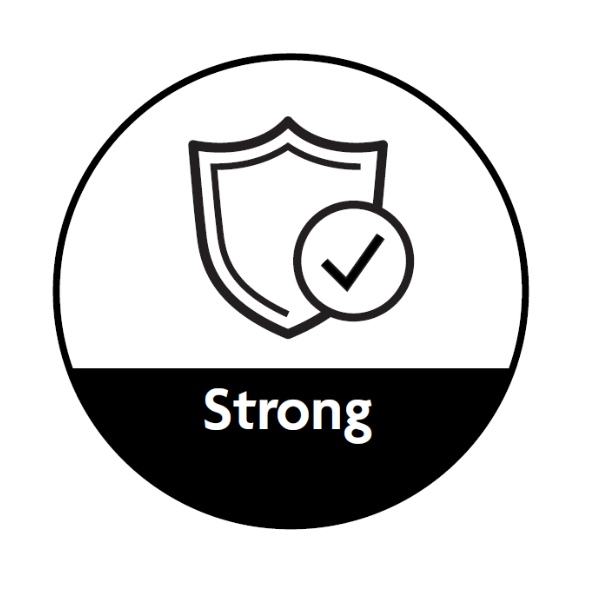
Strength: Despite their lightweight nature, marine composites provide excellent strength and structural integrity.
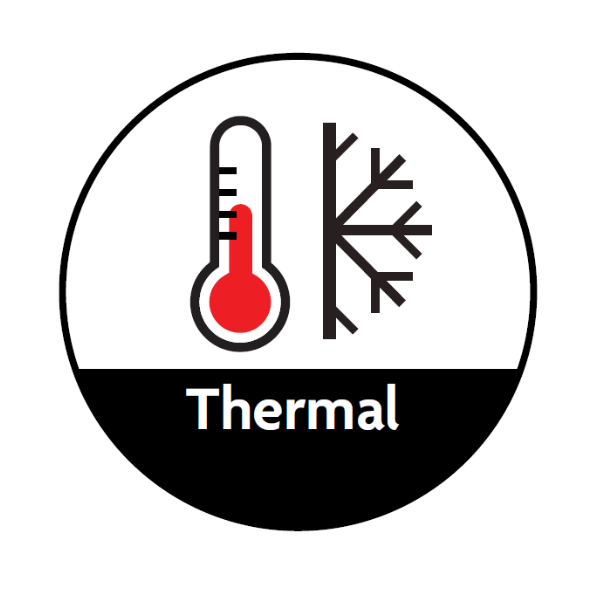
Thermal Insulation: Superior thermal insulation properties help maintain internal temperature stability in marine vessels.
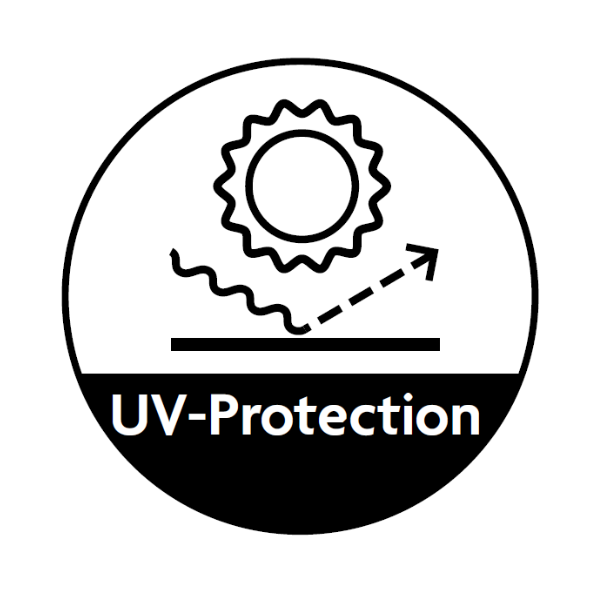
UV Resistance: Marine composites are resistant to ultraviolet degradation, maintaining their strength and appearance even with prolonged sun exposure.
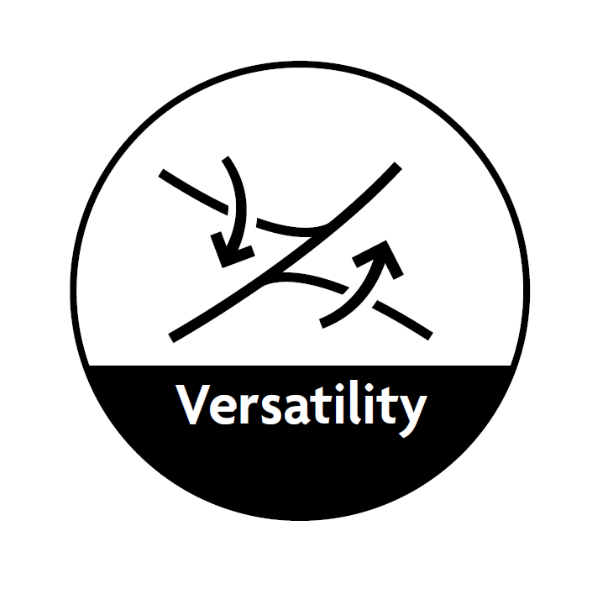
Versatility: Their adaptability allows them to be easily moulded into complex shapes, enabling more innovative designs and custom solutions.
Fibreglass: The Accidental Revolution
One of the most widely recognised marine composite materials is fibreglass. Its discovery was unintentional researchers, experimenting with glass fibres to replace mineral wool insulation, stumbled upon its superior properties. Fibreglass quickly became a staple in the marine industry, and today, it is used in over 90% of yachts. Its success lies in its balance of affordability, strength, and durability.
Two main types of fiberglass are commonly used in marine applications: E-Glass and R-Glass (S-Glass). E-Glass is the standard for composites due to its affordability, strength, and resistance to environmental factors. However, R-Glass, or Strength Glass, surpasses E-Glass in both strength and toughness, though it comes at a much higher cost.
Carbon Fibre: Performance at a Premium
While fibreglass paved the way for marine composites, carbon fibre took things to a new level. Known for its exceptional strength-to-weight ratio, carbon fibre is about six times more rigid than E-Glass and far lighter than steel or aluminium. These properties make it a favourite in high-performance sailing vessels, luxury yachts, and powerboats.
Despite its many advantages, carbon fibre’s high cost presents a challenge. However, the demand for its unmatched strength and lightweight qualities continues to grow. Carbon fibre also presents handling risks due to the fibrous nature of the material, which can cause harmful dust particles to become airborne. These challenges necessitate additional safety measures during manufacturing, which can further drive-up costs.
Aramid: Strength with a Caveat
Aramid, a synthetic polymer, became popular around the same time as carbon fibre. The most well-known member of the Aramid family is Kevlar®, but others like Nomex® are also utilised in marine applications. Aramid offers remarkable strength and durability without adding weight. However, it has one significant drawback—it can absorb water, which is far from ideal for marine use. For this reason, Aramid is typically used in conjunction with other composite materials that protect it from moisture.
Sandwiching: Combining Strength and Affordability
Given the expense of advanced composites like carbon fibre and Aramid, engineers have developed a technique known as sandwiching. This process involves placing a core of less expensive material, such as foam or balsa wood, between two layers of composite. The result is a material that is thicker and more rigid without the excessive cost. Sandwiching also helps distribute stress across a larger area, reducing the risk of damage from impact.
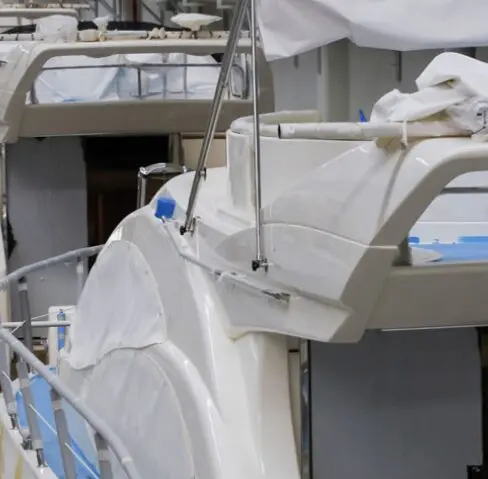
The Future of Marine Composites
The marine industry continues to evolve, with ongoing research into new composite materials that could offer even greater strength-to-weight ratios. Advances in technologies like carbon nanotubes are pushing the boundaries of what’s possible, promising to enhance durability, reduce costs, and improve safety.
To view more articles by DTC click here: Insights Archives | DTC (dtc-uk.com)