Stepping into the world of manufacturing of composites, it is like a fast-forward into the future of automotive design. We are seeing serious trends and innovations, where automotive composites are turning the industry on its head. The focus is on making cars lighter, zippier, and more planet friendly through sustainable composites. So, read on as we explore how automotive composite materials are reshaping the way we hit the road.
The rise of manufacturing of composites in the automotive sector
Although composites first began use in the 1950s in high-end sports and luxury vehicles such as the 1953 Chevrolet Corvette, which featured a fibreglass-reinforced plastic body, the journey to wide-scale adoption has taken many decades. The widespread, heavy use of composites in vehicle manufacturing began to take off in the 1980s and 1990s. During this period, advancements in the manufacturing of composites technology, coupled with the automotive industry’s growing focus on fuel efficiency and performance, led to a greater adoption of these materials from composite manufacturers.

Throughout this article, we explore why composite materials have risen in popularity in the automotive sector. Appreciated for many decades for their toughness and lightness, the adoption of electric vehicles and technological advances in composite science is only increasing the desire of vehicle manufacturers to use this exciting materials technology.
Key reasons for the automotive industry’s switch to composite materials
So, why are automotive manufacturers focused on using composites in manufacturing? Here are some of the reasons:
- Better safety features – composite materials are tough, they absorb collisions well, keeping all vehicle occupants much safer
- Cost-effective in the long run – the upfront cost of composites is often higher, but they offer high ROI across the lifecycle of usage through lower maintenance and running costs
- Design flexibility – designers can get creative as the materials are much easier to mould into a range of aerodynamic shapes
- Eco-friendly options – another reason for adoption is their eco-friendliness. Manufacturers are already producing natural fibre composites and bio-based green composites (e.g., made from flax or hemp fibres). These natural fibre composites are renowned for durability & longevity, their energy efficiency in production, being lightweight, often embrace recyclability & reusability, and usually have reduced lifecycle emissions
- Enhanced performance – cars with composite parts handle like a dream. They are more responsive, faster to accelerate, and are typically more fun to drive
- Improved fuel efficiency – the lower weight to develop composites simply equates to less fuel being needed per mile driven
- Increased durability – cars need to last, and composites do not disappoint. They resist rust and corrosion, meaning your car stays looking fresh for longer
- Innovation in materials – the automotive world’s always looking for the next big innovation, and composites are it. Composite manufacturers are innovative and are opening doors to new technologies and materials that are pushing cars into the future
- Reduced manufacturing time – time is money. Composites are quicker to work with and speed up the whole car-making process
- Weight reduction – lighter cars are the future, and composites are like the ultimate diet plan for vehicles. They cut down the weight, making cars more fuel-efficient and nippier on the road
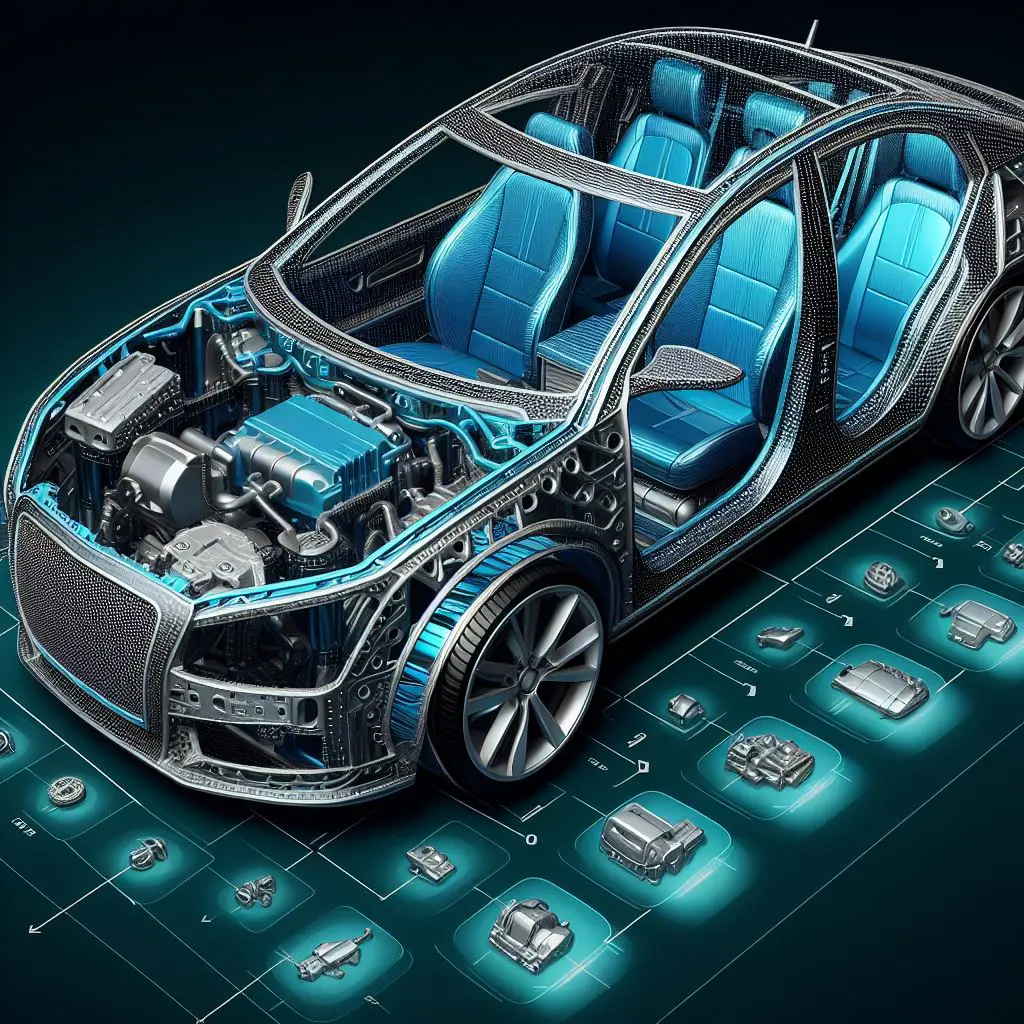
Types of composites used in automobiles
Carbon fibre and fibreglass are clearly the frontrunners in terms of composite usage, but below we list five composites used regularly in automotive manufacturing:
- Carbon fibre – is a polymer material (and is short for CFRP (carbon fibre reinforced polymer)), which is both incredibly lightweight and strong, so has a high strength-to-weight ratio. Compared to steel, for example, carbon fibre is twice as stiff and five times stronger. Carbon fibre, therefore, is popularly used for other composite structures for high-performance and luxury vehicles
- Fibreglass – in many different automotive applications, such as to form automotive interior panels, auto parts, and insulation, general fibreglass is a common material. Its superior strength, low weight, resistance to corrosion, and thermal insulation qualities are all present. The most widely used materials in the automotive industry are still steel and aluminium, but the use of fibreglass products in the building of vehicle superstructures is growing, although replacing steel structural elements can be challenging from an upfront cost-perspective
- Kevlar – DuPont™ Kevlar® fibres are actively used in high-performance automotive components for their strength, temperature resistance and numerous other attributes. Kevlar is used in automotive sector components such as belts, brake pads, clutch plates, filters, gaskets, hoses, and tyres
- Graphene – is increasingly adopted in the automotive industry for a wide diversity of uses. Applications include electrically conductive coatings and packaging, exterior cladding, fire-retardant components, Li-ion batteries (in electric cars), sound protection foam and many other applications too
- Polymer Matrix Composites (PMCs) – a variety of polymer composites, which are frequently used in various automotive parts. PMCs provide a versatile balance of strength, and weight, accompanied by cost competitive composite solutions
Innovations by composite manufacturers for cars
The world of automotive composites is constantly evolving with significant technology advancements. This includes materials and methods that are making cars lighter, stronger, and more efficient than ever before. From space-age materials to technology that sounds like it is straight out of a laboratory, these innovations are totally reshaping how cars are built and how they perform. It is not just about looking sleek; it is about pushing boundaries and turning the future of car design on its head.
Cutting-edge automotive composite applications
In the fast-paced world of car manufacturing, composites are the unsung heroes, silently revolutionising how cars are made and function. Below we explore some of the latest and greatest applications that are seriously transforming the automotive industry:
- 3D printed composites – bringing precision and customisation to a new level, 3D printing with composite materials is transformative in vehicle design
- Bio-based composites – made from natural fibres, these green composites reduce the carbon footprint without compromising on quality
- Carbon fibre reinforced plastics (CFRP) – super light yet tough, CFRP is revolutionising car bodies for better performance and fuel efficiency
- Hybrid composites – mixing different types of fibres, these composites offer the best of all worlds for tailored car part performance
- Nano-composites – tiny but mighty, nano-composites are enhancing material properties like never before, from strength to heat resistance
- Self-healing composites – just like it sounds, these materials can repair themselves, making car bodies more durable and long-lasting
- Smart composites – embedded with sensors, these materials provide real-time data on car performance and structural integrity
- Thermoplastic composites – quick to mould and recycle, thermoplastic composites are speeding up production and making cars more eco-friendly
Composite materials and electric vehicles
Composite materials are making a major difference in the electric vehicle (EV) manufacturing industry. An important contributor is the lightweight nature of composite materials, which very much plays hand in hand with the green credentials of electric vehicles. The lighter weight (such as lightweight EV battery enclosures) means less battery power is needed and therefore, less charges between journeys. Composites are a major support in promoting electric vehicles as a mainstream alternative to internal combustion engine (fossil fuel powered) vehicles.
Composites are also a critical ally in vehicle handling and speed. This makes them fun and very efficient to drive. Composite materials also extend the life of electric vehicles, due to the increased durability and tough-wearing nature of the materials. So, not only do they help electric vehicles go the extra mile (quite literally), but they also ensure these cars stay on the road longer, which is a win for both your wallet and the planet.
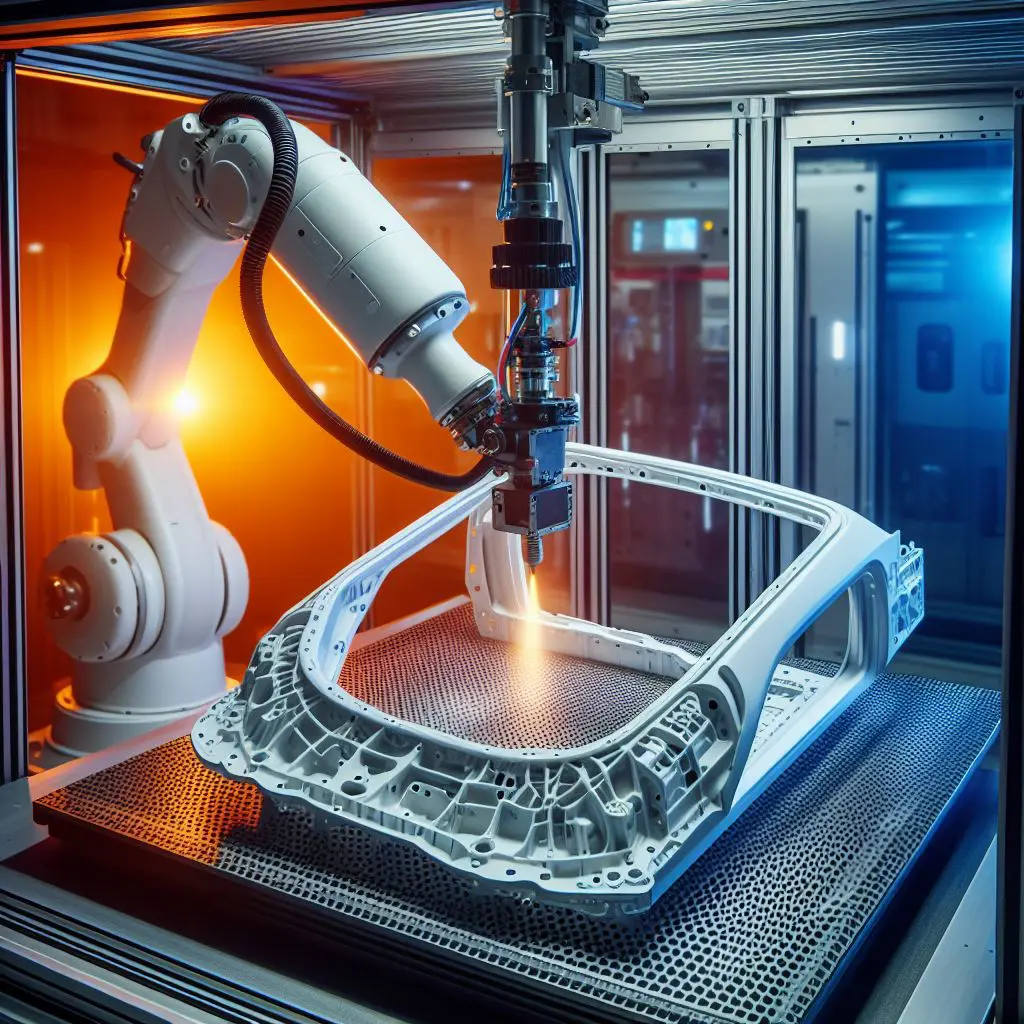
The future of automotive composites
What does the future hold for the manufacturing of composites? Well, to some extent we can forecast this now as some technological innovations are already here (you will see some of these mentioned above). Listed below are just some (and certainly not all) innovations in the automotive composites industry:
- 3D printing revolution – additive manufacturing (also called 3D printing) is already transforming composite manufacturing. This technology is ideally suited to custom vehicle parts manufacturing, ensuring that parts (particularly low production volume vehicles) are faster to make and more affordable
- AI-enhanced composites – AI has a role to play in the composite manufacturing industry with a range of smarter materials being manufactured for optimal performance
- Eco-friendly composites – the world is driving for increased eco-friendliness and the composite industry is no different. Increasingly sustainable composites are being made from a higher percentage of sustainable and eco-friendly sources
- Integration with other technology – composites will not just be about the material. Composites will be part of a larger technology ecosystem embedded in vehicles and will work alongside sensors and many other smart technologies
- Lighter and stronger – there is a never-ending quest for lighter, but stronger composites. Equally true in the aviation and aerospace sectors, future composites will go even further in reducing weight but increasing strength and in doing so will improve vehicle efficiency
- Self-healing materials – this sounds a bit futuristic, but self-healing materials are here now! Imagine composites that self-heal such as with bumpers, a healing agent which repairs scratches and dents in car bodywork or perhaps car frames which are protected from becoming deformed
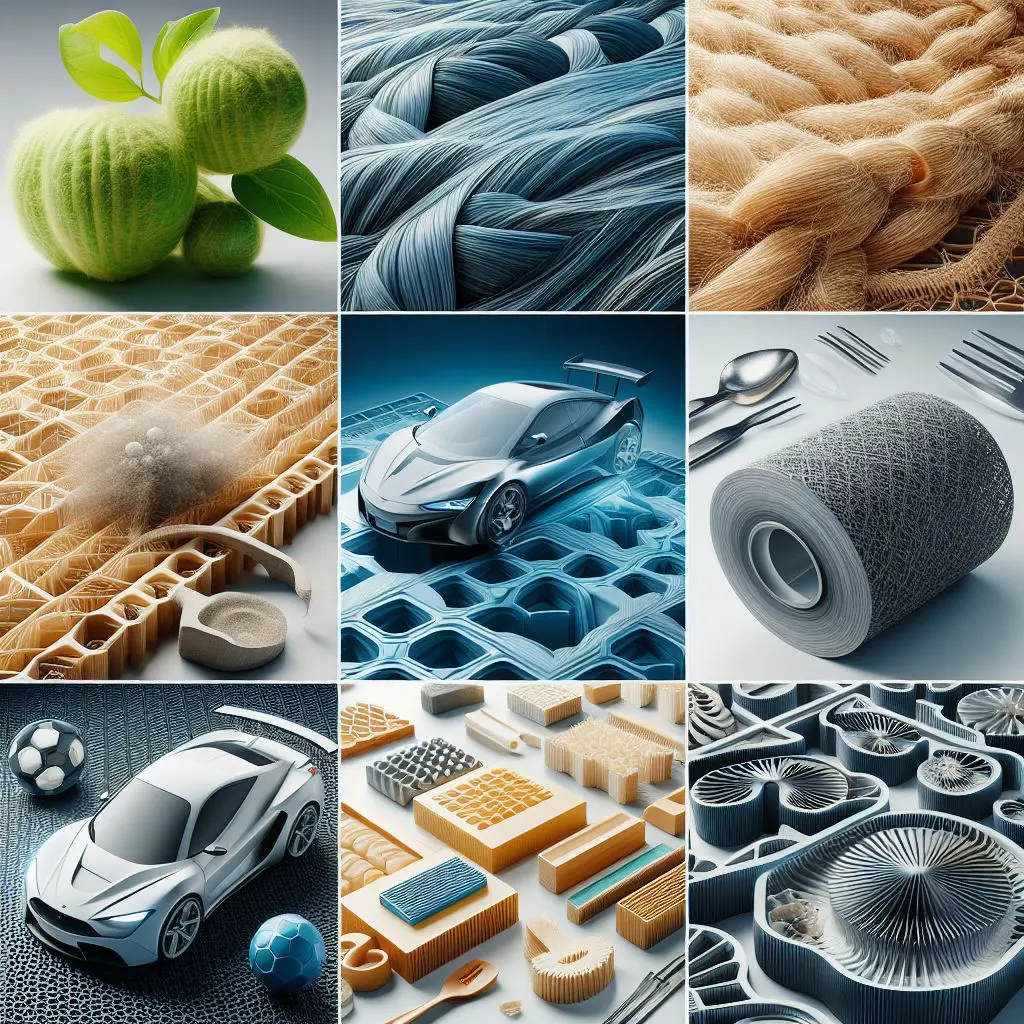
Conclusion
Well, we have travelled back from the classic days of the 1953 Corvette to the super advanced cars we see today. Composites like carbon fibre and natural fibres are totally changing composite manufacturing, making cars lighter, stronger, and kinder to our planet. From the way composite battery enclosures power up electric vehicles to the sleek designs of automotive interior panels and conventional body panels, it is clear these materials are the future.
In the world of low production volume vehicles, composites are a secret weapon, offering top-notch performance without weighing cars down. And let us not forget the role of polymer composites in making cars more durable and eco-friendlier. It is no longer about just about getting from A to B; it is about doing it in style and with a conscience.
Looking forward, the road seems exciting with composites steering the way. We are talking about materials that are not just building cars but redefining them, bringing together technology, sustainability, and some serious style. So, keep your eyes peeled, the future of cars with composites at the helm is going to be nothing short of amazing.
Contact DTC
The manufacturing of composites advances at pace, particularly in the field of automotive composites. With electric vehicles seeking a minimal carbon footprint, sustainable composites are highly sought after.
Join the DTC Hub today and we can supply you with competitively priced automotive composite supplies including just-in-time stock management, rapid ordering, with scan & go capability and much more.
View hundreds of composite materials at great prices when you visit https://www.dtc-uk.com/composite-consumables-materials/. As automotive specialists, you can also view automotive knowledge centre articles here.
Contact DTC using these methods:
- Phone – 023 8025 1100
- Emails – send these to sales@dtc-uk.com
- Contact page – click this link